I PIONIERI DEGLI STAMPI PER CERAMICA
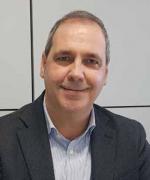
Come ha affermato il presidente Michele Gatti, fondatore
di Gape Due S.p.A., lei è una delle colonne portanti dell’azienda, la prima
produttrice di stampi per l’industria ceramica per fatturato e numero di
clienti, nel distretto più importante al mondo per il settore. Quando è
incominciata la sua avventura in questa azienda? Nel 1999, fui assunto come
disegnatore all’ufficio tecnico. Dopo tre anni, in seguito alla decisione strategica
dell’azienda di espandersi nel mercato italiano, mi fu data l’opportunità di
vedere all’opera gli stampi che disegnavo: assumendo il ruolo di tecnico
commerciale, potevo seguirne il funzionamento nelle fabbriche dei clienti e
capire se ci fosse qualcosa da migliorare in base alle esigenze specifiche di
ciascuna commessa. Michele Gatti è stato il primo produttore di stampi per
ceramica a istituire la figura del tecnico commerciale e questo ha permesso
alla Gape Due di aumentare notevolmente il numero dei clienti italiani,
soprattutto fra le realtà industriali più importanti del distretto: visitare il
cliente una o due volte la settimana, oltre che rispondere alle sue chiamate,
contribuisce a fidelizzare il cliente più di qualsiasi altra azione commerciale.
Noi siamo considerati interlocutori strategici, perché siamo sempre vicini ai
clienti e alle loro esigenze. Nel servizio prevendita, aiutiamo il cliente a
scegliere la tipologia di stampo più adatta alle proprie esigenze produttive di
volta in volta, riducendo in questo modo le problematiche cui potrebbe andare incontro.
Nel servizio post-vendita, poi, lo aiutiamo a calcolare l’effettiva necessità
delle scorte, in modo da ridurre gli sprechi, anche perché noi siamo
strutturati per soddisfare le richieste di consegne urgenti, oltre a fornire
tempestiva assistenza tecnica.
Parlando e ascoltando, sorgono anche idee nuove. Quali
sono le principali innovazioni nate da esigenze specifiche del mercato a
partire da quando lei ha incominciato a lavorare qui? Se facciamo
riferimento agli ultimi vent’anni, sono state tre le tappe salienti dell’innovazione.
Nel 2002, la Gape Due ha messo a punto e brevettato lo stampo Multiformato, che
ha comportato un notevole risparmio di tempo per le fabbriche di piastrelle, perché
consente di produrre diversi formati, sostituendo alla pressa soltanto alcuni
inserti: la matrice, infatti, è costruita per alloggiare griglie porta- lastrine
sfilabili, le Drawer Liners, predisposte per una tipologia di formato, ma
sostituibili, insieme ai tamponi, direttamente sullo stampo per produrre il
formato sottomultiplo.
Già questo all’epoca è stato un grande passo, il secondo è
stato, invece, lo stampo isostatico Calibra, nato nel 2013 grazie
all’attenzione che abbiamo sempre posto verso gli sviluppi del settore e alla
nostra costante attività di ricerca. Calibra è in grado di garantire
l’uniformità della densità di pressatura sia su formati medio piccoli – con più
uscite piastrella – sia su formati grandi, come quelli che vengono realizzati negli
ultimi anni. Le tendenze della moda sono andate sempre più verso grandi e
grandissimi formati e questo ha rappresentato un’autentica sfida per chi realizza
stampi, ma siamo riusciti a vincerla con macchinari e investimenti adeguati
alla produzione di formati fino a 90x180 cm. Inoltre, Calibra garantisce un’estrema
versatilità per rispondere all’esigenza delle industrie ceramiche di soddisfare
le richieste più disparate dei loro clienti, che non sono più standard, ma
cambiano in modo importante e repentino.
Oggi, siamo attrezzati con impianti che ci consentono di
realizzare ogni tipo di stampi compatibili con le presse esistenti. Oltre al
formato, un’altra variabile in evoluzione è lo spessore: ormai fra un tipo di
piastrella e l’altra ci sono differenze importanti, si va da pochi millimetri
fino a due centimetri e oltre. Tuttavia, con pochi particolari costruttivi di
differenza fra un caso e l’altro, siamo in grado di offrire la migliore
tecnologia per realizzare qualsiasi spessore.
Ma la svolta decisiva nell’innovazione è intervenuta quando,
nel 2017, anche grazie agli incentivi del programma Industria 4.0, abbiamo brevettato
lo Smart Mould, lo stampo intelligente che si avvale della sensoristica più
avanzata per soddisfare le esigenze della fabbrica digitale. Lo Smart Mould
permette il monitoraggio continuo del ciclo produttivo dello stampo, rilevandone
i parametri di funzionamento. I dati sono visualizzati ed elaborati da un pc
industriale, con interfaccia semplice e intuitiva, che è in grado di fornire
all’operatore a bordo macchina un efficace e immediato strumento di
monitoraggio del processo produttivo, allertandolo in caso di malfunzionamenti,
prima che essi possano influire negativamente sull’esito della pressatura del prodotto
ceramico; inoltre, è possibile gestire la tracciabilità e lo stato di vita dei
macchinari (stampi/tamponi) e ottimizzarne il processo di rigenerazione.
Questi i primi tre passi importanti nel cammino della nostra
impresa, ma non ci fermiamo qui, stiamo lavorando alla quarta innovazione,
perché se un’azienda si ferma incomincia ad andare indietro. E noi non possiamo
permettercelo: dobbiamo raccogliere i frutti di oltre mezzo secolo di vita e gettare
i semi per i frutti che raccoglieranno le nuove generazioni.