IL DISTRETTO DELLE CERAMICHE E LE SUE MACCHINE
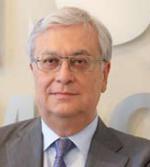
Chissà
che cosa direbbe Leonardo da Vinci dinanzi all’alta ingegneria delle macchine
costruite dalla BMR per la produzione di piastrelle in ceramica, o dalle altre
aziende del distretto di Sassuolo aderenti all’Acimac (Associazione costruttori
italiani di macchine e attrezzature per la ceramica), di cui lei è stato eletto
presidente lo scorso giugno…
Leonardo da
Vinci ha progettato macchine impensabili per l’epoca e ci ha lasciato
un’eredità straordinaria, fatta d’ingegno, di scienza, di arte e di cultura,
con cui dobbiamo confrontarci ancora oggi. Tuttavia, credo che, se per assurdo tornasse
in vita e venisse a visitare le nostre fabbriche, sarebbe sorpreso soprattutto
per la grande varietà di macchine scaturite dalla fantasia dei nostri
costruttori per rendere la produzione delle piastrelle sempre più tecnologica,
industrializzata e automatizzata, e sempre più attenta alla salute dei
lavoratori e dell’ambiente. E forse noterebbe il fermento che alimenta il
nostro distretto e che ne fa quasi una comunità scientifica e tecnologica,
oltre che un polo produttivo di riferimento mondiale, dove l’emulazione verso
l’eccellenza è costante, fin dagli anni Cinquanta, quando le aziende nascevano
da una chiacchierata al bar fra amici, che diventavano soci il giorno dopo.
Chi non ha
vissuto nel nostro comprensorio, chi non si è cimentato in qualche modo
nell’esperienza delle ceramiche non riesce a capire il valore aggiunto insito
nella memoria, che si tramanda proprio come una tradizione. Per questo,
nonostante ormai le industrie ceramiche siano sorte in tante nazioni e siano in
grado di copiare i prodotti italiani in poco tempo, una piastrella “made in
Sassuolo” si distingue da tutte le altre per un contenuto culturale inimitabile,
che è diventato un marchio di qualità. Del resto, anche se l’origine delle
piastrelle di ceramica come prodotto di uso domestico si può fare risalire
almeno al IV secolo a. C., quando in Egitto erano utilizzate per decorare vari
tipi di casa, le prime vere e proprie industrie per la produzione del gres
rosso sono nate qui, grazie alla grande disponibilità di argilla sulle nostre
colline. E qui sono intervenute le evoluzioni del prodotto che hanno portato
dalla bicottura alla monocottura e, infine, al gres porcellanato, che ci ha
fatto conquistare un primato assoluto.
Le
industrie ceramiche che hanno contribuito a far nascere questo distretto hanno
sempre trovato nelle aziende costruttrici di macchine, come la BMR, partner
affidabili per il proprio sviluppo e per la qualificazione del proprio prodotto.
Quando architetti e designer apprezzano gli effetti di splendide superfici levigate
e smaltate per i loro progetti di arredamento moderno e funzionale; quando i
pavimenti e le pareti si vestono di un look che conferisce stile, classe ed
eleganza alle nostre case, forse dovremmo pensare alle macchine costruite proprio
per rispondere alle novità che il mercato richiede o per anticiparne le tendenze,
facendo scuola.
Può citare
qualche esempio di applicazione dei vostri macchinari nella filiera produttiva
di un’industria ceramica?
In quasi
cinquant’anni, ci siamo specializzati nella costruzione di tecnologie
industriali per levigare, squadrare e lucidare superfici in ceramica. A oggi,
possiamo dire che le principali industrie ceramiche in Italia e all’estero
hanno installato nei loro stabilimenti le nostre linee di lappatura, taglio e
squadratura. In questi ultimi anni, è aumentata la richiesta per le linee di
taglio e rettifica per lastre di grande formato (fino a 1600x3200 mm), che
rappresentano la tendenza più attuale. Addirittura, alcune industrie hanno
convertito interi stabilimenti ai nuovi formati e noi abbiamo fornito macchine
di rettifica per il gres porcellanato interamente a secco, come la Top Squadra Dry,
insignita di importanti riconoscimenti e menzioni per il suo valore tecnologico
ed ecosostenibile. Un’altra tendenza che sta prendendo piede è quella dei
listelli effetto legno e, anche in questo caso, la nostra tecnologia si è
adoperata per contribuire alla realizzazione dei nuovi formati richiesti dal
mercato.
Oggi gli
impianti BMR sono installati in vari paesi, soprattutto nei mercati degli Stati
Uniti, della Russia, del Brasile e del Far East asiatico. Ma com’è nato il vostro
Gruppo e come si è sviluppato?
BMR
Costruzioni Meccaniche è nata negli anni settanta, a Scandiano, nel cuore del
comprensorio, con l’obiettivo di costruire macchine di carico/scarico e linee
di smaltatura. All’inizio degli anni Novanta, ha deciso di dedicare parte delle
proprie risorse alla lavorazione meccanica dopo cottura delle piastrelle. Sono nate
così le prime rettifiche squadratrici- bisellatrici, dedicate in particolare al
gres porcellanato, fra cui la squadratrice Syncrobelt®, che ha riscosso un
immediato interesse del mercato. Nel 2004, l’Azienda, ormai affermata come
partner primario per l’impiantistica meccanica delle grandi industrie
ceramiche, ha deciso di acquisire la Cemar, azienda di Schio (VI) specializzata
nella produzione di levigatrici per il settore ceramico. Con l’esperienza del
partner acquisito, BMR si è posta sul mercato come player di riferimento per il
fine linea per la produzione ceramica, aggiungendo alla fornitura di linee di
levigatura e squadratura complete per gres porcellanato un’importante gamma di
teste di lucidatura, satinatura e lappatura, sia dei porcellanati tecnici sia
di quelli smaltati. Grazie all’elevato contenuto tecnologico dei macchinari
made in Italy, interamente progettati e realizzati nei due stabilimenti di
Scandiano e Schio, l’azienda oggi riveste un ruolo di leadership che le
consente un investimento costante in ricerca e sviluppo, con risultati
importanti sia nell’innovazione sia nell’attenzione all’ambiente.
Il 2015 è
stato un anno record per Acimac: le aziende a essa associate hanno aumentato il
fatturato fino a superare i livelli pre-crisi del 2008. E anche le industrie
ceramiche hanno registrato un incremento. Quanto è servito puntare sulla
qualità del design italiano per il rilancio?
Puntare sul
contenuto di design è sempre vincente, soprattutto in un momento in cui sono
ampiamente utilizzate le tecnologie digitali, che consentono di imitare
perfettamente i materiali naturali, come la pietra o il legno. Lo sviluppo
della tecnologia digitale ha offerto nuove possibilità, ma rischia di
appiattire il mercato perché permette ai concorrenti di imitare una piastrella
in tempi molto brevi. Pertanto, occorre operare anche su lavorazioni diverse
dal digitale, così da rendere più difficile l’imitazione. La standardizzazione
deve lasciare più spazio all’artigianalità e, perché questo accada, occorre
tornare a investire nella ricerca sulle piastrelle, anziché adagiarsi sugli
effetti ottenuti con la riproduzione digitale, che pure ha rappresentato una
rivoluzione importante nel settore.
Se n’è
discusso anche in un convegno che si è tenuto nell’ambito della recente edizione
di Tecnargilla, la più importante fiera al mondo per la fornitura all’industria
ceramica e del laterizio, organizzata da Acimac e Rimini Fiera, ogni due anni,
per proporre il meglio dell’innovazione estetica e di processo per il settore. Com’è
andata quest’anno?
Oltre a presentare
le novità più interessanti delle aziende espositrici, ha attirato un elevato
numero di operatori internazionali: 16.764 (il 6,3 per cento in più rispetto al
2014) buyer stranieri, su un totale di 33.395 visitatori (il 4 per cento in più
rispetto al 2014). Anche fra i 500 espositori ospitati, il 40 per cento
proveniva da circa 25 nazioni, su un’area di circa 80.000 mq, suddivisa in
quattro sezioni espositive: Tecnargilla, dedicata alle tecnologie per
piastrelle, sanitari e stoviglieria; Kromatech, la vetrina del colore e della
creatività in ceramica; Claytech, la sezione dedicata alle tecnologie per il
laterizio; T-White, la nuova area espositiva dedicata alla produzione di
macchinari e impianti per la produzione di sanitari e stoviglieria in ceramica.
A
proposito d’internazionalizzazione, la BMR quest’anno ha aperto una sede in
Tennessee, a Dickson, nella “Ceramic Valley” americana, dove, nel corso degli anni,
avete installato oltre venti linee complete presso le più note e influenti realtà
ceramiche della zona…
È una sede
logistica, aperta in collaborazione con LB di Fiorano Modenese, con lo scopo di
portare l’innovazione della tecnologia made in Italy in America, offrendo la competenza
e la professionalità di settore al mercato locale, attraverso un servizio di
assistenza tecnica e commerciale immediata al cliente. Inoltre, volevamo
offrire un upgrade tecnico-qualitativo dei processi di produzione delle
industrie ceramiche USA, assecondando i principi di efficienza energetica e
produttiva che sono i capisaldi della nostra continua ricerca tecnologica.