RCM: L'INDUSTRIA DELLE MACCHINE FATTE A MANO
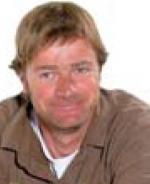
La R.C.M.
– una delle prime fabbriche italiane di motoscope e lavasciuga – con lei è alla
quarta generazione. In che anno e in che modo ha preso le redini della
produzione, per proseguire il contributo che la famiglia Raimondi ha dato
all’industria meccanica fin dal lontano 1899, anno in cui il suo bisnonno Ippolito
avviava la produzione artigianale di biciclette a Parma?
Dopo avere
lavorato per alcuni anni come responsabile dell’ufficio tecnico, settore di cui
ora è responsabile mio padre Renzo, nel 2009 fui incaricato di organizzare il
layout dello stabilimento di via Radici a Casinalbo di Formigine (MO), dove avremmo
trasferito la produzione, che fino a quell’anno era rimasta nella sede storica
di via Tiraboschi, attualmente sede amministrativa. Pur essendo delle stesse
dimensioni del precedente, il nuovo stabilimento avrebbe ospitato una linea di produzione
in più, inoltre, aveva un magazzino meno ampio e non poteva usufruire del
magazzino esterno che utilizzavamo in via Tiraboschi. Quindi la sfida non era
piccola.
E in che
modo è riuscito a vincerla?
Abbiamo
rivoluzionato completamente la gestione e la programmazione dei rifornimenti.
Aumentando la rotazione del materiale, abbiamo ottenuto un doppio beneficio:
abbiamo ridotto lo spazio necessario al magazzino interno e siamo riusciti a
creare una linea di produzione in più. In questo modo, si è abbassato anche il
valore del magazzino, diminuendo notevolmente i rischi di un’esposizione
finanziaria elevata, che, soprattutto nei momenti di difficoltà di mercato come
quelli degli ultimi anni, sono decisamente da evitare.
Come
hanno risposto a questa rivoluzione coloro che dovevano provvedere più
velocemente all’approvvigionamento dei materiali?
Ho assunto
io stesso l’incarico della programmazione e sono passato da una cadenza
semestrale a una trimestrale, fino ad arrivare oggi a una programmazione
mensile. Negli ultimi due anni, abbiamo avuto un portafoglio ordini da uno a
due mesi, mentre nei primi anni della crisi avevamo un portafoglio ordini a un
mese scarso. I fornitori hanno dovuto trasformare parecchio la loro gestione,
perché il cambiamento è stato notevole e non tutti sono riusciti a seguirci, in
quanto non tutti erano in grado di fornire il materiale in tempi brevi. Adesso
che il mercato, in generale, è molto più rapido e richiede sempre più una
produzione just-in-time, noi siamo stati avvantaggiati, perché abbiamo
anticipato la tendenza, istruendo i nostri fornitori ad avere tempi di reazione
diversi, anche se non è stato facile e immediato farlo capire loro.
Quali
sono i materiali che acquistate dai fornitori?
Noi
produciamo solo il 10 per cento dei componenti delle nostre macchine, quindi il
ventaglio di fornitori è molto ricco e variegato. Nel settore della meccanica
in particolare, i fornitori sono molto specializzati o sono riuniti in un
cartello di distribuzione abbastanza ampio. Allora, poiché ciascun componente richiede
il rapporto con un fornitore specifico, noi ne abbiamo circa tremila, anche
perché spesso abbiamo il doppio fornitore per uno stesso componente, sia per
metterli in concorrenza sia per evitare di rimanere sprovvisti di qualche pezzo
importante.
Come
hanno reagito i collaboratori al nuovo layout dello stabilimento?
In realtà,
l’abbiamo costruito insieme. Dopo avere eseguito la mappatura dello
stabilimento, l’ho sottoposta ai vari responsabili di linea e di magazzino, con
i quali ho condiviso gli obiettivi fin dal primo giorno. Se le linee sono rimaste
invariate dal 2009 è anche perché non ho imposto assolutamente nulla, ma ho
ascoltato i loro suggerimenti e così ho evitato che, in seguito, qualcuno mi
attribuisse la responsabilità per eventuali scarse funzionalità organizzative nel
lavoro.
Quali
sono state le principali difficoltà da quando è diventato responsabile di
produzione?
La
difficoltà maggiore per me rimane a tutt’oggi la gestione dei collaboratori
che, nonostante abbiano dai venti ai cinquant’anni, a volte hanno un approccio infantile
ai problemi relazionali. I problemi tecnici si risolvono, ma quelli umani sono
i più difficili, e non hanno età. Questo è uno dei motivi per cui mi reco spesso
nelle linee di produzione, perché per me è importante parlare con ciascuno dei
miei dipendenti, per accorgermi subito se qualcosa non va, senza aspettare che si
crei un problema. E per questo sono abituati a chiamarmi e a dirmi se qualcosa
non va fra loro. Ma questo non vuol dire che senza di me si fermi tutto. Non ho
mai voluto che succedesse una cosa simile e so che posso fidarmi in modo
assoluto dei responsabili e di persone che lavorano qui da molti anni.
Infatti,
se avete un’anzianità lavorativa elevata, l’ambiente di lavoro deve essere più
che soddisfacente…
Noi non
abbiamo catene di montaggio e anche i tempi di produzione li abbiamo rilevati a
partire dal ritmo che riescono a mantenere in media le persone che lavorano in
ciascuna linea. Inoltre, le nostre macchine sono montate singolarmente, in
quasi tutti i modelli, e questo contribuisce a dare all’operatore maggiore
responsabilità, ma anche maggiore gratificazione.
Ecco
perché nelle interviste precedenti abbiamo sottolineato l’artigianalità
industriale a proposito delle vostre macchine, quasi fatte a mano…
Sono
veramente fatte a mano, al 100 per cento. Noi diamo le istruzioni sugli
standard da rispettare e il montatore deve fare in modo che la macchina superi
la prova del collaudo.
R.C.M.
vanta una vasta gamma di quasi cento fra tipi e modelli di macchine. Quali sono
i modelli che ha progettato lei quando lavorava all’ufficio tecnico?
L’Alfa, la
Slalom e l’Atom Plus.
Qual è
l’innovazione del modello Alfa, per esempio?
Quella che
abbiamo chiamato Smart Traction, “trazione sveglia”: anziché una sola spazzola,
l’Alfa ne ha due controrotanti che, mentre ripuliscono il pavimento, fanno
anche avanzare la macchina. È la prima macchina con il telaio completamente rotazionale,
costruita con un materiale plastico, che rende facile l’uso e la manutenzione;
inoltre, con i suoi comandi intuitivi, può essere usata senza istruzioni
particolari, è leggera da guidare e quindi non affatica l’operatore. Non
ultimo, ha il vantaggio di essere molto economica all’acquisto perché altamente
industrializzata.
Quali
sono le principali soddisfazioni che le ha dato il suo lavoro dal 2009 a oggi?
Soddisfazioni
ne ho avute tante, fin da subito, appena ho constatato che lo stabilimento
funzionava bene. La più bella soddisfazione comunque è arrivata con i risultati
dell’anno scorso, in cui abbiamo prodotto 350 macchine in più dell’anno
precedente impiegando lo stesso personale. Per noi, che produciamo 4000 macchine
all’anno, 350 macchine in più fanno la differenza. Ma anche avere ridotto
l’esposizione del magazzino di un milione di euro è stata una bella
soddisfazione, nonostante abbiamo aumentato la produzione.
Quali
sono i programmi per i prossimi mesi?
Stiamo
avviando la produzione di una macchina particolare, di cui finora abbiamo
prodotto solo nove esemplari all’anno: quest’anno dovremmo passare a cinquanta,
destinati al mercato tedesco. Questa è la prossima sfida e abbiamo dovuto allestire
una linea dedicata e formare diverse persone per raggiungere questo obiettivo.
Anche
lei, come suo padre, corre con le auto storiche di famiglia o ha qualche altro
hobby?
Prima
correvo, ma ormai partecipo solo a tre o quattro gare all’anno. L’altro mio
hobby invece è lo sci, che è stato anche una professione. Ho fatto persino
carriera come atleta fino all’età di ventidue anni e sono stato in squadra con
Alberto Tomba. Poi sono diventato maestro di sci, ho avuto una scuola per
tredici anni, avevo anche un negozio di noleggio sci: tutte attività che mi
hanno dato una formazione che mi è stata utile anche in azienda. Adesso non ho
più la scuola, perché era troppo impegnativa, ma insegno come libero professionista,
perché ho molti clienti che seguo nei weekend.
Ha
incominciato a sciare da bambino?
Ho iniziato
a tre anni, come tutti i miei cugini, perché i fratelli Raimondi – Renzo,
Romolo e Roberto –, tra l’altro, costruivano skilift. Romolo è stato anche
campione regionale di discesa libera, ma tutti i fratelli partecipavano alle
gare di sci e ci hanno trasmesso questa passione.
È una
bella esperienza. Tra l’altro, la parola sport deriva dal latino “diporto” e
indica movimento fuori dalle mura della città. Per chi ama la meccanica forse non
è casuale l’impegno nello sport…
La pratica
di uno sport ha due facce: se da un lato aiuta a imparare l’importanza delle
regole, dall’altro impedisce alle persone di stare ferme, insegna quella spinta
al movimento costante che non le abbandona più. Lo sport è una scuola di vita,
insegna che, per ottenere un risultato, occorre darsi da fare, perché nessuno
regala niente. E lo sci, inoltre, è uno di quegli sport in cui si capisce che
il giudizio è del tempo, non di qualcuno che ti considera più o meno bravo,
perché i risultati sono misurati da un cronometro, non da una giuria.
Comunque, ho sempre portato anche nel mio lavoro la
tendenza a non stare mai fermo e a seguire l’occorrenza, senza mai fissarmi in
un ruolo: attualmente sono responsabile di produzione, ma se valutassimo che
occorre il mio impegno in altri reparti, per esempio, in quello commerciale, non
sarebbe un problema imparare ciò che occorre per ottenere risultati anche come
agente. Mi piace anche fare cose nuove e non mi pongo limiti, assolutamente.